专题
[摘要]今年3月份,精朗科技效率200ppm的圆柱电池自动化装配线正式下线。该圆柱电池自动化装配线主要用于圆柱26650电池生产,如今该装配线已正式交付给客户,效率稳定在180PPM。后期经过优化调试后,可达到200PPM甚至更高。
伴随着全球新能源车的放量增长,当前车企正面临着动力电池产能不足、芯片供应短缺等多重难题。这样的行业背景之下,动力电池企业纷纷出台扩产计划。据不完全统计,仅今年首季度,以比亚迪、欣旺达、中创新航、亿纬锂能等为代表的动力电池企业已相继公布多个新投建项目,整体投建资金高接近3000亿元,规划新增产能接近600GWh。
而与此同时,为保障动力电池的稳定供应,国外包括特斯拉、大众集团;国内包括广汽埃安、蔚来汽车等车企,争相自研自建电池厂,推动着动力电池产能不断爬升。根据研究机构的预测,2025年全球动力电池总产能将增长至2042GWH,这也意味着未来三年内累计新增的电池产能将超过1500GWH,相关锂电设备企业也即将迎来新的发展机遇。0
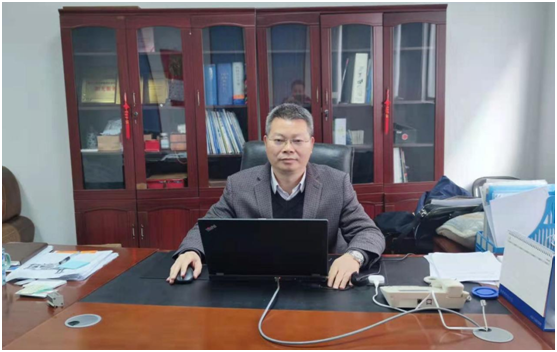
精朗科技总经理黄轶
作为业内领先的设备供应商,深圳市精朗联合科技有限公司(下称“精朗科技”)成立于2008年,公司专注于锂电池先进、高效、自动化设备的开发、制造及销售,主打产品为锂电池全系自动化注液线,包括高压等压式、钟罩式、腔体式、转盘式等品类。此外精朗科技还涉及圆柱电池自动装配线、方形电池自动装配线、软包电池自动装配线等。
精朗科技总经理黄轶表示,注液作为锂电池生产工序中关键环节,对锂电池生产效率以及品质、电化学性能、安全性等均有着重要的影响。因此选择高精度、高效率、高可靠性的注液设备,已成为主流锂电池生产企业共同选择。对注液设备企业而言,在保障注液精度与速度前提下,如何匹配锂电池规模化制造新需求,成为大家必须正视的课题。
加速推进注液设备国产化
回顾精朗科技的发展历程,就是一部有关锂电注液设备的进化史。2009年精朗科技成功压发了旋转阀式电动注液泵;2011年精朗科技60PPM转盘注液机成功面世;2013年精朗科技推出高压等压注液技术;2015年精朗科技推出方形电池高压等压注液机;2017年精朗科技推出国内首创钟罩式高压等压注液机;2019年推出铝壳圆柱高压等压注液机等。
值得注意的是,精朗科技不仅参与见证了锂电注液设备的技术进步,而且在多个领域精朗科技都属于首创。这其中就包括国内首创30PPM-18650转盘注液机、国内首创60PPM转盘注液机、国内首创高压等压注液技术、国内首创钟罩式高压等压注液机及铝壳圆柱电池高压等压注液机等。而正是这些突破性技术,推动着国内注液设备不断向前发展。

钟罩式高压等压注液机
同时在推动锂电注液设备国产化方面,精朗科技同样功不可没。黄轶提到,在精朗科技成立之初,国内锂电池企业主要使用的是加拿大海霸的注液设备。精朗科技成立不久便成功推出60PPM转盘注液机,凭借着优异的性价比,对海霸注液机进行替代。可以说精朗科技在推动注液设备国产化及提升国内注液设备整体水平方面,均做出了应有贡献。
随着新能源车发展的不断深入,对于电池性能的要求越来越高。而注液的精度、速度和稳定性直接影响着电芯的品质和生产效率,而要保障注液精度和速度就要对注液设备的性能进行革新,这也对注液机设备企业提出了挑战。这样的背景下,精朗科技通过技术创新和产品升级,成功开发出高压等压注液技术,并将其应用到方形、圆柱各个领域。
据黄轶介绍,精朗科技国内首创的高压等压注液技术,可大大提升注液效率。与此同时等压技术可以对电池内部和外部同时加压,有效解决了传统注液设备在注液过程中,因为电池内部与外部压力的差异导致的鼓包、漏液问题,大幅提升了注液良品率,产品良率可提升至99.9%以上。而且该系列注液机可实现标准化和模块化生产,换型非常方便。
凭借着优异的产品性能,精朗科技的设备得到国内众多主流电池企业认可,无论是在客户使用案例方面,还是交付数量方面在业内均处于领先地位。这其中就包括宁德时代、蜂巢能源、比亚迪、欣旺达、国轩高科、亿纬锂能、比克电池、中航锂电、瑞浦能源、珠海银隆、捷威动力、力朗电池等。而时至今日,精朗科技客户群体仍在持续扩张中。
黄轶表示,动力电池企业产能大规模提升和产品性能提升的需要,正在倒逼锂电设备企业进行工艺革新并持续丰富产品矩阵。首先在效率方面,动力电池单线产能从此前的3GWh向着10GWh迈进,这就要求锂电设备生产效率相应提升3-5倍;其次在智能化方面,TWh时代的到来要求锂电池产线智能化、自动化水平更高,驱动锂电设备智能化升级。
应对这样的发展趋势,精朗科技每年会投入营收的10%作为研发费用,并组建了一支高素质的研发团队,通过不断技术创新,打造先进可靠的设备,为客户创造更高附加值。如今精朗科技的注液设备,在精度、效率、可靠性、技术先进性方面已媲美日韩,获得相关专利30余项。黄轶提到,精朗科技下个目标是研发300PPM的圆柱电池注液设备。
200PPM装配线成功下线
除为客户提供高端智能化注液设备外,精朗科技在锂电池自动装配线方面也早有布局。早在2018年,精朗科技开始推出整套电池自动装配线并被相关电池企业采用。以铝壳电池组装线为例,其包括揉平机、包浆机、入壳机、正负极集流焊盘机、合盖预点焊机、封口焊接机、前氦检、密封钉焊机、后氦检等,为客户提供打包式的完整的解决方案。

精朗科技全极耳电池揉平设备
黄轶表示,近几年来国内锂电池生产水平逐年提高,带动着相关的锂电设备水平不断地向前发展。截至目前包括涂布、模切、注液、干燥、检测等在内的前中后段设备中,已分别出现能够媲美日韩先进设备的企业。不过在电池后段生产装配线方面,却还存在着比较明显的差距。而这其中,效率和稳定性是国产装配线亟待突破的重点和难点所在。
资料显示,目前日韩圆柱电池自动装配线具备180-200ppm的生产效率,而国内设备的效率只能做到100-120ppm。虽然当前国内有少数企业在进行200ppm圆柱电芯后段装配线的研发,但整体来说效果并不理想。造成这种情况的原因除技术水平差异外,还与国内前后端设备不匹配关系密切。这种不匹配往往会导致效率低下,且设备调试时间过长。
在黄轶看来,当前国内圆柱电池自动化装配线的性能并未完全发挥出来,仍然存在着很大的上升空间。如果可以释放出设备的固有性能,将生产效率、稳定性等指标做到和日韩企业同等水平。同时在提升效率和控制成本上多下功夫,才能建立起自己的先发优势,从而打造出属于国产设备的核心竞争力,只有这样才会有替代进口设备的市场机会。
而精朗科技通过不断的技术探索,有望成为首个吃螃蟹的企业。今年3月份,精朗科技效率200ppm的圆柱电池自动化装配线正式下线。据了解,该圆柱电池自动化装配线主要用于圆柱26650电池生产。该装配线自立项到正式下线历经1年时间。如今该装配线已正式交付给客户,效率稳定在180PPM。后期经过优化调试后,可达到200PPM甚至更高。
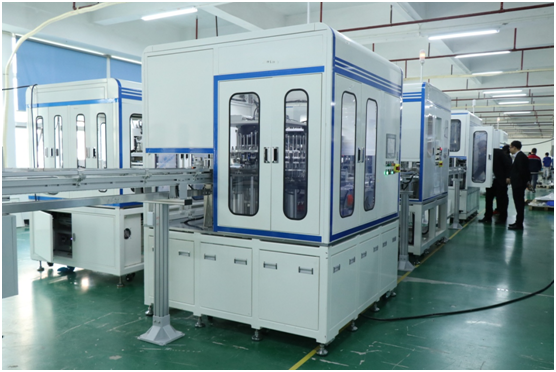
200ppm自动化装配线
黄轶表示,该圆柱电芯后段装配线主要包括的上料设备、全自动封口设备、自动焊盖帽焊接设备、注液设备、滚槽检测设备、负极点焊设备、自动入壳设备、清洗设备、套膜设备以及OCV检测设备等,几乎全部来自于精朗科技,不会存在设备不匹配的问题,而且成本得到大幅下降。预计到明年,精朗科技将着手于300PPM圆柱电池装配线的研发。
值得注意的是,在降成本压力的推动下,现如今4680大圆柱电池已经成为电池企业追捧的对象。2020年9月,特斯拉首次披露了4680电池的相关技术。随后包括比克电池、亿纬锂能、宁德时代、松下以及LG等电池企业,已对4680电池展开积极布局,预计到2023年形成规模化生产。而对于当前火热的4680电池,精朗科技也有技术方面的储备。
黄轶提到,4680电池采用无模组设计,不用再遵循组到块、块到包的形式,而是直接将电芯进行分布排列。这样的好处是不仅能够省掉很多工序,实现高速生产,而且在装配线的投入方面更少,对于电池企业来说诱惑力巨大。当前精朗科技已经能够提供4680电池装配线的整线(中试线)或分段设备,而且还有4680设备的相关专利正在申请当中。
随着新能源车市场的逐步恢复,以及新能源车补贴政策延续的预期,锂电设备行业景气度有望持续。而得益于行业高景气度,精朗科技设备订单饱满。据黄轶透露今年精朗科技营收有望突破7亿元。而为了配合公司发展需求,精朗科技也在积极扩大产能。现如今精朗科技已拥有光明总部,深圳玉律、东莞寮步两大生产基地,年产值超过10亿元。
黄轶最后认为,随着锂电池发展不断深入,锂电设备的设计要预先考虑其延展性,不仅体现在尺寸的延展性,还包括工艺、智能化、模块化、制造化和数字化的延展性,要从衔接的合理性、兼容性及切换的灵活性等多维度来布局未来的设备工艺。放眼未来,精朗科技将不断加大研发投入,有计划地推进产品创新迭代,以满足日益变化的市场需求。
转载请注明出处。
1.本站遵循行业规范,任何转载的稿件都会明确标注作者和来源;2.本站的原创文章,请转载时务必注明文章作者和来源,不尊重原创的行为我们将追究责任;3.作者投稿可能会经我们编辑修改或补充。